Resource efficiency and circularity
To decouple increased material use from growth, we begin by optimising raw material use and minimising production waste. We examine every stage of our product’s life cycle to find opportunities to apply the circularity principles: recycling materials, extending product lifespan, lightweighting and seeking renewable alternatives to fossil-based materials.
We transform our business to decouple it from resource constraints
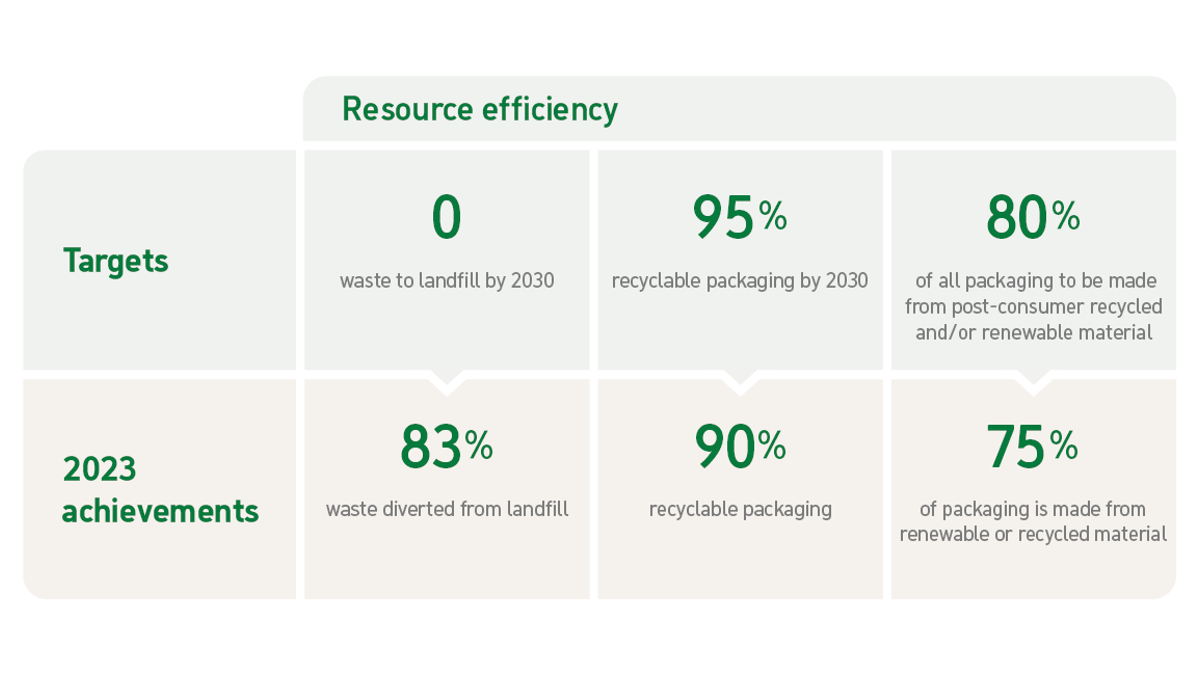
-
Our position statement on resource efficiency and circularity
Mölnlycke's ambition to decouple material use from its growth goes beyond recycling. It all starts with limiting the need to recycle. Therefore, we focus on zero waste, working in accordance with the ‘right first time’ principle and repurposing and reclaiming materials.
We’re on a journey to become a zero waste company, which involves focusing on both waste and water. We have an ambitious target of zero waste to landfill by 2030 as well as reusing water at all our most water-intensive sites by 2030 and we implement closed water loop systems in our production environments to that end.
Our waste reduction management programme to achieve the targets is based on site-specific activities designed to avoid waste being created in the first place and then minimising waste to landfill by correct segregation and disposing of remaining waste. We also identify new outlets for materials that would otherwise have been disposed of. Our actions make an important contribution to the UN Sustainable Development Goal on Sustainable Consumption and Production (SDG 12). To find out more, please see our integrated Annual and Sustainability Report 2023.
Our medical solutions often contain plastic or are delivered in diverse plastic packaging, with unique intrinsic performance properties which extend the lifespan of our solutions and protect them from external factors such as damage during transport and handling, or deterioration caused by contamination. This reduces the need for additional raw materials and resources in our products and contributes to minimising our customers’ waste.
As part of our resource efficiency journey, we have an ambition to provide >95% recyclable packaging by 2030. Governments around the world are adopting legislation targeted at tackling, for example, plastic waste. By embracing the power of upstream innovation to achieve two key circular economy innovation strategies — elimination and material circulation — we stay ahead of the curve. We continuously work together with customers, suppliers, recyclers, universities, and other partners to develop innovative and circular packaging solutions that have lower holistic environmental footprints and enable our customers to be more sustainable and deliver on their sustainability ambitions. These include a growing share of lighter, recyclable, recycled, bio-based and biodegradable solutions while guaranteeing best clinical outcomes.
We consider competition with the food chain when evaluating the use of bio-based renewable raw materials and preferentially select ISCC certified biobased materials, guaranteeing a transparent traceability along our supply chains and meeting the environmental and social standards.
In addition, we take a proactive approach to identify, manage and remove hazardous substances in all our products and processes to ensure safe use, ahead of legislation, future-proofing our products against changes in regulations.
We substantiate our research and efforts into alternative feedstocks and circularity of our products or packaging by continually updating our product Life Cycle Analyses.
We further increase the existing activities aimed at preventing littering, including educational projects for our customers and local communities in the countries in which we operate.
Key levers to responsible consumption and production
-
Re-gauging materials to minimise end user waste
-
Designing devices with longer service life
-
Introducing post-consumer recycled and renewable raw material, certified by ISCC or FSC
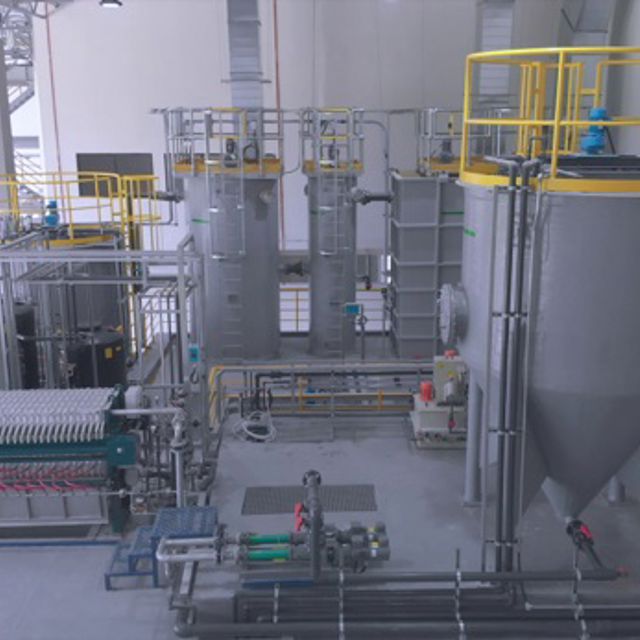
Water: promoting best practices
Water plays a crucial role in various Mölnlycke activities, including raw material production, product manufacturing (such as foam production), cleaning, cooling, and sanitation. In particular, glove production is a water-intensive process. Our Kulim Hi-Tech Park glove manufacturing plant in Malaysia is LEED-certified and received the highest possible score in the water efficiency category.
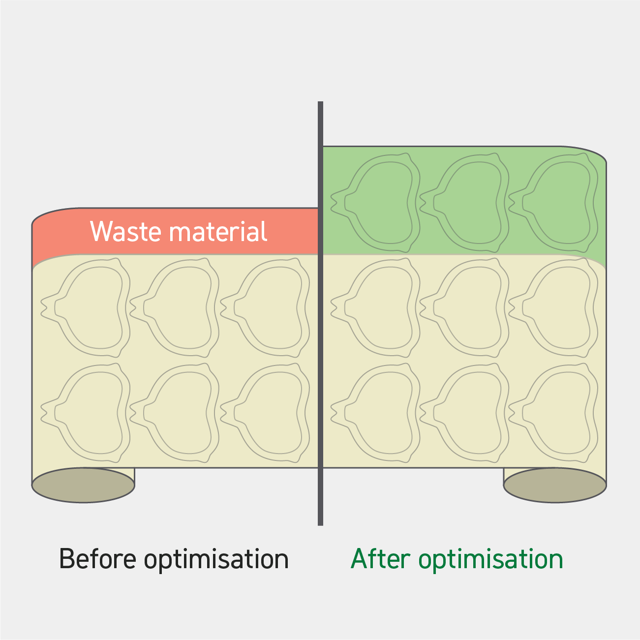
Waste reduction through manufacturing innovation
With the improved wide-cut process the factory in Maine reduced the amount of waste sent to landfill by 30 tonnes per month. The optimisation also increased the number of dressings produced from one roll by 50%.
Helping customers reduce waste
Studies show that switching from single-packed medical supplies to our customisable Mölnlycke® ProcedurePak trays can reduce packing waste with up to 90 %, while saving valuable time in preparation.